Ashgabat Textile Complex – Enterprise With No Analogues in CIS
The enterprises belonging to the Textile Complex serve as a bridge in offering consumers finished products processed from harvested cotton.
Achieving a diverse portfolio of textile products has a positive effect on the profitability of the business, and a modern approach to the areas of product sales and marketing leads to an increase in the number of foreign markets expressing interest in the products.
Representatives of the Business Turkmenistan agency visited the production facility of the Ashgabat Textile Complex (ADT), which, due to the quality of textile products and distinctive marketing methods, has continued to strengthen its position in the international textile market in recent years.
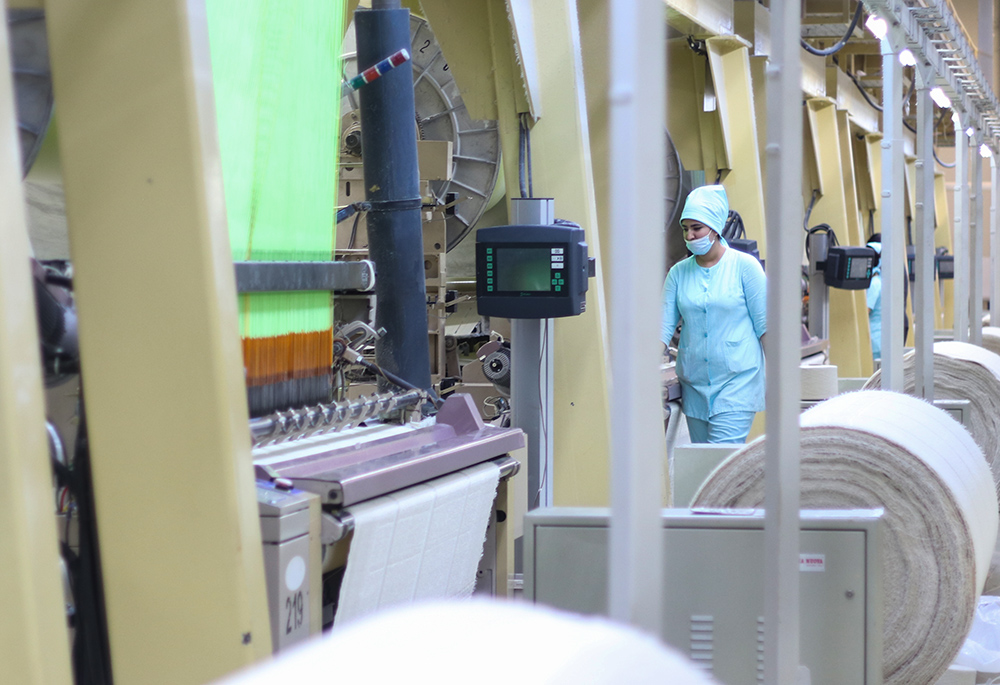
During the production tour, our guide was a specialist of the complex Azatdurdy Berjanov, who told us about the features of the enterprise, which has no analogues in the CIS countries in terms of production capacity.
The cotton yarn wound that enters the production chain forms various napkins, terry towels used in the home and bath, beddings, and soft children’s toys at the end of the process. They are then sent to the finished goods warehouse of the complex.
ADT employs over 2800 workers, most of which are women. The specialists’ uniform color varies depending on the workshop where they work.
This textile complex makes a worthy contribution to the diversification of products obtained from Turkmen cotton. Recently, ADT launched production of the first organic products in Turkmenistan. The complex is also the first manufacturer of soft toys in Turkmenistan. Currently, the complex is preparing to release a large batch of new products under the trademarks Vada and Goza.
The construction and equipment of the Ashgabat textile complex was carried out in 2 stages. The first stage of the complex was commissioned in February 2007, and the second in October 2013.
The complex has the annual capacity to process 13,100 tons of cotton yarn and 22.5 million square meters of raw cotton fabric.
The ADT, covering a total area of 37 hectares, consists of spinning, weaving, dyeing and sewing facilities.
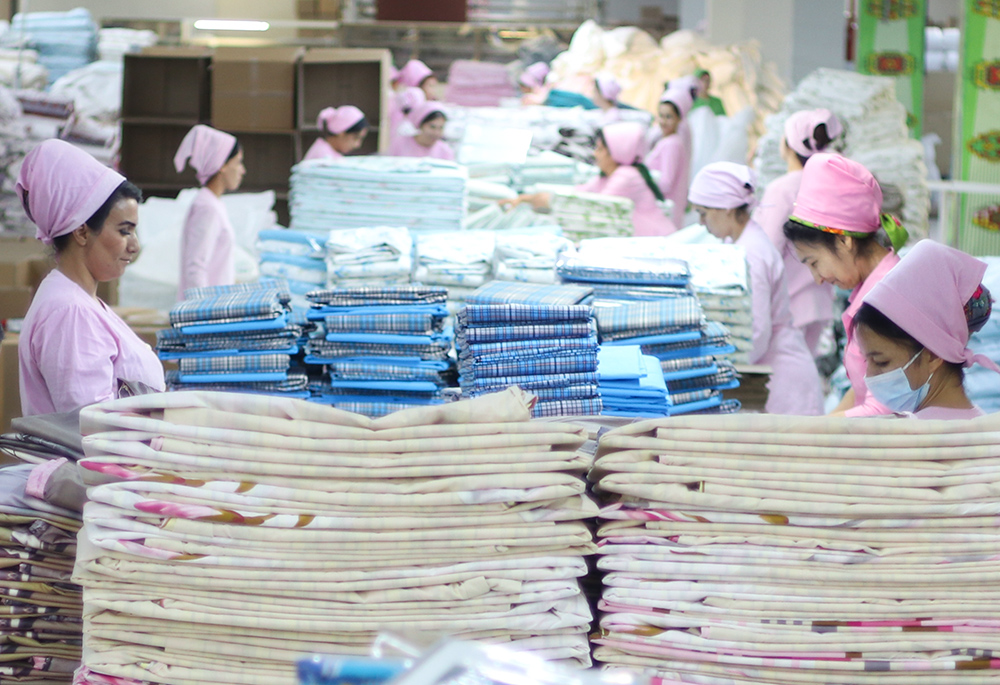
The spinning facility of the complex is equipped with automated machinery from leading manufacturers as Tsudakoma (Japan), Brückner (Germany), Karl-Mayer (Germany), Staubli (Switzerland), Pentek (Italy), and Dilmenler (Turkey). In the main facility workshop, yarn for fabric is wound in 2 methods. The facility uses Tsudakoma TWS-E 100/2400 equipment in cotton spinning.
The yarn that has passed through warping equipment is starched in special chemical solutions to ensure strength in the textile manufacturing process.
Next, the yarn is dyed in the desired color. Karl-Mayer equipment is used in the production fabrics from dyed yarn. These fabrics form 20% of all terry fabrics produced in the complex.
Finished yarn is sent to the weaving facility. The first and second stages of the weaving facility of ADT are capable of producing about 5 thousand tons of raw pile fabric per year and 55,8 million square meters of raw cotton fabric per year. The department employs 260 units of weaving equipment, 38 of which weaves fabrics using the jacquard weaving method, and 222 – using the reinforcement method. Equipment that works with jacquard weaving method allows to place 3D patterns on the surface of the fabric. The complex, with the use of this equipment, mainly produces luxury fabrics for hotels.
The equipment used in the second stage of the complex, commissioned in 2013, was selected at the international exhibition ITMA-2011, held in the Spanish city of Barcelona.
From the weaving department, fabrics are sent to the dyeing center. This facility is capable of dyeing 4,900 tons of terry fabrics and 70.6 million cotton fabrics per year. With the help of installed machinery in the department, various patterns can be applied to the surface of cotton fabrics. The facility dyes satin, jacquard-satin, ranfors, creton, and flannel.
The ADT sewing facility uses Juki sewing machines for straight seams and overlocks. The facility annually produces 4,680 tons of terry products and 19.8 million pieces of finished garments. The sewing department of the complex has special sewing machines for the production of bedding sets and terry napkins. Finished products are then sent to the packaging facility, where they are packed in ordinary and gift packaging.
The company offers its customers textile products under the ADT trademark. The textile complex also produces products for well-known foreign brands, such as the Turkish brand TAÇ.